On the 11th, 12th, and 13th of August 2020 and 1st, 2nd, 3rd of September 2020, I attended the Green Belt Public Training organized by MBizM Group Sdn Bhd, which was held at the Best Western Hotel Petaling Jaya for the first session and Hilton Hotel, Petaling Jaya for the second session. The participants consist of two green belters and four black belters (there were an additional of five black belters on the 4th day of every session) from various industries and positions. The Green Belt Public Training & Black Belt Accelerated training was a whole day programme from 9 am to 6 pm. The Green Belt public training aims to improve process performance, deliver medium to high impact projects and achieve significant cost savings.
Introduction
The public training was handled by MBizM Group’s consultant, Dr. Muraliraj. The first session of this training was held in Best Western’s Hotel seminar room. In order to follow the standard operating procedure before entering the seminar room, the temperature was taken to make sure everyone was in pristine health condition. Dr. Muraliraj, as the trainer, introduced himself to the participants, and an ice-breaking session was carried out where each participant was asked to introduce a person sitting next to him/her, their name, place of work, and what they expect to learn throughout the training. To be frank, I am quite nervous about attending this training as I never have any experience with Lean Six Sigma before, but I believe it is going to be an exciting learning journey for me.
First Session
After the introduction and ice-breaking were done, Dr. Muraliraj started on the first chapter about the history of Lean and Six Sigma. He also explained about what Lean is and its purpose. Since it is just the first day, we have not gotten into the tough part of the training just yet, so I was relieved! Other than that, we learned about three types of process; Value Adding (VA), Value Enabling (VE) and Non-Value Adding (NVE), seven types of waste, and the Critical to Quality (CTQ). On the second day, I learned about the Six Sigma methodology to solve business problems on existing processes, which is Define, Measure, Analyze, Improve and Control (DMAIC). Dr. Muraliraj taught us about the Define phase and the tools to use to define problems and goals. The tools that we learned during the Define phase were the Drill Down Tree, Pareto Charts, Kano, SIPOC and Financial Benefit Estimation, Cost of Poor Quality (COPQ).
On the second day, we learned about the Measure phase; How to measure current process capability or performance with root cause analysis tools; fishbone, 5 why, 3×5 why and XY Matrix. Not only that, we also learned about data collection plan, detailed process map and risk assessment by using the Failure Mode and Effects Analysis (FMEA). After lunch, we did some activities about the root cause analysis to understand how to use the fishbone diagram better, we were divided into two groups and each group consist of 3 participants.
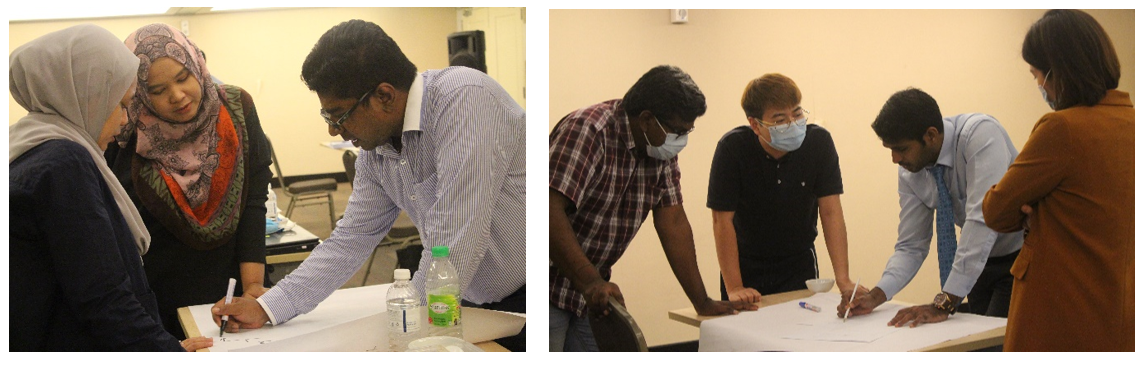
Activities done during the first session
The measure phase is when we started to learn about basic statistics. I was quite nervous! Looking at the word statistics made my heart beat fast because the last time I learned about statistics was years ago back in the university. Luckily it was just the basic ones where Dr. Muraliraj explained about mean, median, mode, and average. He also taught us about understanding the normal curve and standard deviation in process capability and diagnosing capability issues using Cp, Pp, Cpk, and Ppk. On the third day, we learned about the Analyze phase in DMAIC. This phase is to analyze factors by identifying the vital few factors. This was the day when we learned about statistics fully and using Minitab for data analysis. We also learned about graphical analysis (picture, infographic, run charts, box plots, histograms, dot plots, scatter & matrix plots, and multivari charts) and statistical analysis (hypothesis and regression analysis) to understand the procedures of deciding on whether to accept or to reject the hypothesis to have a valid conclusion.
Second session
On the 1st, 2nd, and 3rd of September, the training resume, but this time was in Hilton Hotel, Petaling Jaya. I kid you not, I bet everyone was so excited when they received an email informing us the venue is changed. Due to unforeseen circumstances, MBizM Group Sdn Bhd decided to change the venue to give all participants the best training experience.
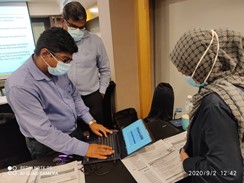
All eyes on the monitor!
In the morning, Dr. Muraliraj recapped the lesson we had learned previously to see whether everyone still remembers what they had learned a few weeks back. On the first day of the second session, we continue learning statistics, yes again. This was the day when we squeezed our brain to the limit. I came from a social science background. Hence, statistics can be pretty hard to swallow. I kid you not! But phew, luckily, Dr. Muraliraj has been a great help as he will try his very best to ensure all the participants will have a clear understanding of implementing statistics in Lean Six Sigma by using Minitab. On the second day, we learned about the Improve phase to improve vital few factors by eliminating its defect and to understand how to generate creative ideas. On the last day of the training, we learned about the Control phase, to be able to establish control plans for continuous management for improved process. As the final rounds came closer, Dr. Muraliraj taught us about Statistical Process Control Introduction (SPC), how to attribute control chart using Minitab. Lastly, Dr Muraliraj taught us about Develop Best Practice transfer and Transferring to Process Owner. On the last day of the second session, exam was held for the green belters.
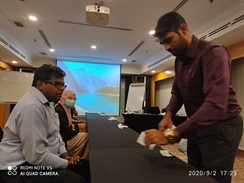
Participan s doing Kanban activity together to undrstand the push and pull method
Conclusion
In conclusion, I can say that joining this Lean Six Sigma Green Belt Public Training by MBizM Group was an eye-opening. I can now understand that Lean Six Sigma Methodology can be applied not just in the manufacturing industry but also in other industries. I am very satisfied, especially with Dr. Muraliraj’s performance throughout the training. He is very dedicated to all the participants and very keen to explain Lean Six Sigma until we can truly understand it. I am also very satisfied with the venue. Well, who does not like it when training was done in a 5-star hotel, right? Overall, I am very happy that I joined this training as I gained Lean Six Sigma knowledge thoroughly.
Testimonial
At the end of the training, we have done some interview sessions with the participants to ask for their opinions about the training.
“The training mets my expectation, I learned lot from Dr Murali. I also learned a lot of new thing, since I am involved in the continuous project improvement at the hospital. I would definitely apply a lot of things that I have learnt at this Lean Six Sigma Training. I actually enjoy the activities very much; it helps me to appreciate the concept and made me remember the knowledge better. Dr Murali give a very good delivery, I really appreciate, he is very helpful. He always relates to our own cases and projects so I really like the way he delivers. Definitely 5 (scale) I really enjoy it and I would recommend it to other people too”- Ms Nur Azida, Pharmacist.